Lean manufacturing principles
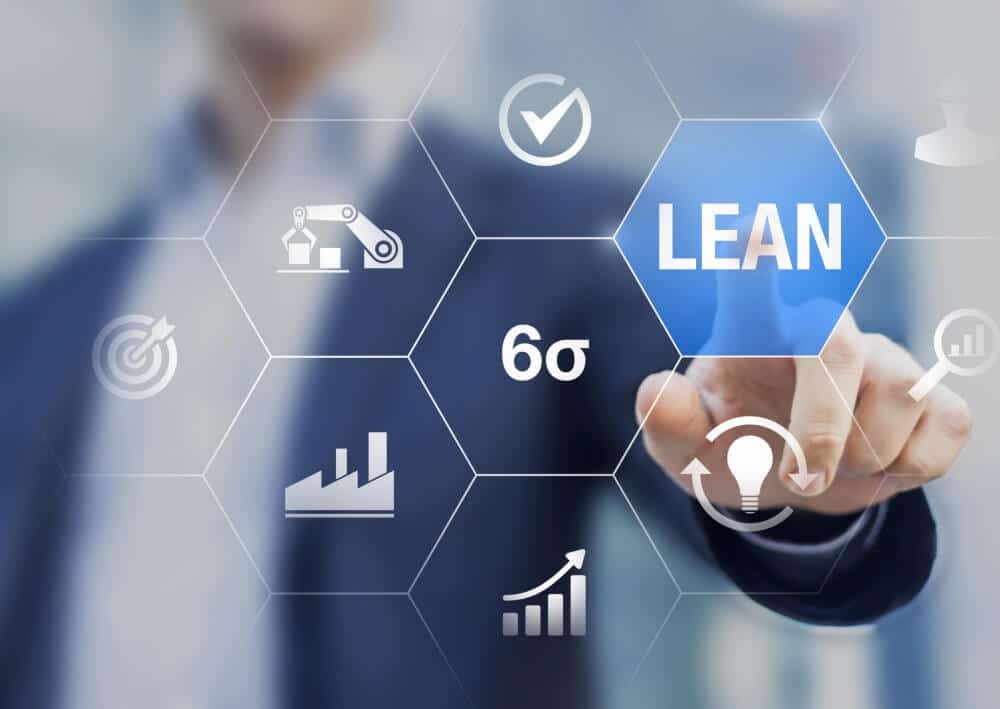
In the fast-paced world of manufacturing, efficiency and productivity are king. One approach that has revolutionized the industry is Lean manufacturing. It's not just a buzzword but a comprehensive strategy aimed at minimizing waste while maximizing value. But what does it really mean to be 'Lean,' and how can businesses effectively implement these principles? This blog post delves into the heart of Lean practices and their transformative power.
Understanding and applying the principles of Lean manufacturing can significantly improve processes, reduce costs, and increase customer satisfaction. By exploring each principle individually, organizations can gain insights into making sustainable improvements. Let's uncover the core elements that make Lean a game-changer in the manufacturing arena.
The Essence of Lean Manufacturing
Lean manufacturing, at its core, is about creating more value for customers with fewer resources. It's a philosophy that sees waste as anything that does not add value to the customer, and it strives to eliminate such waste in all aspects of production. This approach originated in Japan and has since become a global standard for efficiency and quality.
The Lean method recognizes seven types of waste: defects, overproduction, waiting, non-utilized talent, transportation, inventory, motion, and extra processing. Identifying and eradicating these wastes are central to becoming truly Lean.
Implementing Lean practices requires a shift in mindset from traditional manufacturing philosophies. It is not merely about cutting costs but about improving processes to make them more efficient and responsive to customer needs.
By concentrating on value and simplicity, companies can achieve significant improvements in performance, competitiveness, and customer satisfaction.
Principle 1: Identify Value from the Customer's Perspective
The first step in implementing Lean is understanding what value means to your customers. This involves communicating directly with them to comprehend their needs and preferences. The goal is to ensure that every step of your manufacturing process contributes to creating that value.
Value can be in the form of product features, delivery time, price, or quality. It is paramount to clarify these factors and align your processes accordingly.
Failure to accurately identify customer value can lead to wasteful practices, as resources might be expended on aspects that the customer does not value.
Principle 2: Map the Value Stream
Once you understand what your customer values, the next step is to map out every step in your process that contributes to this value. This is known as the value stream. Mapping out these processes can help identify waste and areas for improvement.
A thorough value stream map will include everything from raw material sourcing to the final delivery of the product. This clarity enables organizations to eliminate processes that do not add value.
Common outcomes of value stream mapping include reduced lead times, lower inventory levels, and improved product flow.
Principle 3: Create Flow
Eliminating waste and optimizing your value stream sets the stage for creating a smooth and continuous flow of processes. The goal is to ensure that work-in-progress efficiently moves from one step to the next without interruption or delay.
Critical to creating flow is the idea of pull processing, where production is driven by customer demand rather than forecasting. This minimizes inventory levels and reduces waste.
Improving flow may require redesigning workspaces, adjusting schedules, or introducing flexible workforce practices.
Principle 4: Establish Pull
The pull principle entails producing only what is needed when it is needed, and in the amount needed. This is in stark contrast to traditional push manufacturing, where production is based on forecasts and can lead to overproduction and excess inventory.
Implementing a pull system can drastically reduce waste and lead times by synchronizing production with actual demand.
Techniques such as Just-In-Time (JIT) production are central to achieving an effective pull system in Lean manufacturing.
Principle 5: Seek Perfection
The journey toward Lean is ongoing. The final principle is about continuously searching for ways to reduce waste and improve quality. This requires a culture of continuous improvement where feedback is sought and valued, and employees at all levels are engaged in finding better ways to work.
Lean is not a set-it-and-forget-it strategy; it is a commitment to ongoing improvement. Regular review of processes, listening to customer feedback, and empowering employees to seek out inefficiencies are vital practices.
Striving for perfection might seem daunting, but in Lean, it is about making small, continuous improvements that lead to substantial changes over time.
Implementing Lean manufacturing principles offers a roadmap to operational excellence, significantly impacting efficiency, cost, quality, and customer satisfaction. By focusing on value, mapping the value stream, creating flow, establishing pull, and continuously seeking improvement, businesses can reduce waste and build sustainable processes that thrive in today's competitive market. Lean is not just about doing more with less; it's about creating a culture of excellence that drives innovation and value creation for both the company and its customers.
Related