Quality control and continuous improvement
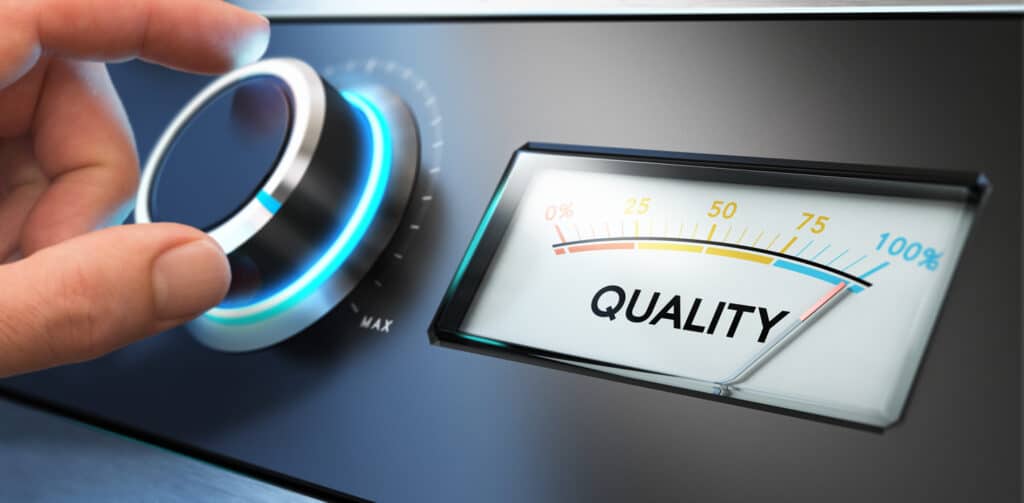
In an era where excellence is expected, understanding the fundamentals of quality control and continuous improvement is not just beneficial but imperative for businesses striving for long-term success. This post delves into these core concepts, offering insights and methodologies to elevate organizational standards.
With a focus on 'Quality' as our guiding principle, we explore various aspects contributing to enhanced performance and customer satisfaction, thereby fostering an environment of relentless advancement and excellence.
The Imperative of Quality Control
Quality control represents a critical component in an organization's quest for excellence, acting as a guardian that ensures products or services meet the stringent standards set forth by the company and expected by the customers. It involves systematic activities designed to determine and maintain the quality of a product.
By implementing effective control mechanisms, organizations can significantly reduce waste, preempt potential flaws, and guarantee that the final outputs meet the required standards. This not only caters to immediate customer satisfaction but also builds a foundation of trust and reliability in the brand.
The process includes various stages, from initial design reviews and regular inspections to testing at different levels of production. Each step serves as a checkpoint to eliminate errors, leading to the consistent creation of value.
Emerging technologies and methodologies, such as Six Sigma and lean manufacturing, have further evolved these processes, offering new ways to achieve even tighter control and higher quality standards.
Embracing Continuous Improvement
Continuous improvement, often aligned with the Japanese term 'Kaizen', is the philosophy of ongoing, incremental enhancement of all aspects within an organization. It stands as a pillar for not just sustaining but also elevating quality over time.
This approach involves everyone within the organization, from executives to frontline employees, each contributing to the collective improvement of processes, products, and services. It's about fostering a culture where innovation and refinement are a constant.
Through tools such as PDCA (Plan-Do-Check-Act), continuous improvement offers a structured methodology for solving problems and optimizing processes. This ensures that improvements are based on data and are aimed at boosting efficiency and effectiveness.
Integrating Quality Control with Continuous Improvement
For an organization to truly excel, it must integrate its efforts in quality control with continuous improvement methodologies. This synergy enables not just the maintenance of quality standards but their enhancement over time.
Quality control ensures that the products or services are up to mark, whereas continuous improvement focuses on making the processes that create those products or services better. When combined, they create a powerful engine driving the organization towards excellence.
Implementing this integrated approach requires a strategic mindset and a commitment to excellence at all organizational levels. Leadership must champion these principles, creating an environment where quality and improvement are embedded in the organizational culture.
Case Studies: Success Stories
Many leading companies across industries have successfully implemented these strategies to achieve remarkable results. One notable example is Toyota, which has become synonymous with quality control and continuous improvement through its Toyota Production System.
Another example is General Electric (GE), which embraced Six Sigma principles to transform its processes, leading to significant cost savings and quality improvements.
These success stories serve as a testament to the value of integrating quality control and continuous improvement efforts, highlighting the potential for transformative change within organizations committed to these practices.
Strategies for Implementation
Adopting these practices requires a strategic approach, starting with leadership commitment and a clear vision. Organizations must create a culture that embraces change and encourages innovation at every level.
Training and education play a crucial role in equipping employees with the tools and knowledge needed to contribute to these efforts. Additionally, establishing clear metrics and feedback mechanisms is essential for measuring progress and identifying areas for improvement.
Finally, leveraging technology and automation can streamline processes, reduce errors, and collect actionable data to inform improvement efforts.
Challenges and Overcoming Them
Implementing these concepts comes with its set of challenges, including resistance to change, lack of clear leadership, and inadequate resources. However, these obstacles can be overcome with effective communication, robust training programs, and incremental implementation strategies.
Engaging employees and making them stakeholders in the process ensures buy-in and fosters a collaborative environment geared towards continuous improvement and quality excellence.
Conclusion
In conclusion, the integration of quality control and continuous improvement is not just a strategy for business success; it's a philosophy that transforms organizations. By focusing on 'Quality' and committing to these principles, companies can navigate the complexities of the modern business landscape, achieving remarkable efficiency, customer satisfaction, and operational excellence.
Embracing these principles requires commitment, strategy, and a culture that prioritizes continuous enhancement. With the right approach, organizations can not only meet but exceed the ever-increasing expectations of quality and performance, securing their place in a competitive global market.
Thus, in the journey towards excellence, 'Quality' serves as both our compass and destination, guiding organizations through the pursuit of perfection in every aspect of their operations.
Related